Improved cost-efficiency and productivity for BASF Shanghai Coatings’ painting plant
New conveyor system in Shanghai enables BASF to meet the market demand
The automotive manufacturing market in China is on the rise. Thus, BASF Shanghai Coatings Co. Ltd. planned an investment to build a new, world-scale automotive coatings plant at the company's existing site at Shanghai Chemical Industry Park in Caojing. The new plant is an expansion of the automotive coatings plant, which began production in 2014 at the same site. In 2016, Lödige Industries was contracted to design, manufacture, deliver, and install a new conveyor system.
The developing automotive industry needs in China
The customer required an expansion of world-scale automotive coatings plant with sufficient capacity. This required close collaboration with the plant operations to ensure safety, high throughput capacity, flexibility and convenience. In addition, the industry needs include the transition from solvent borne to waterborne coatings and from standard primer processes to integrated processes. This reduces overall energy consumption of paint shops thanks to new functionalities of BASF’s coatings solutions.
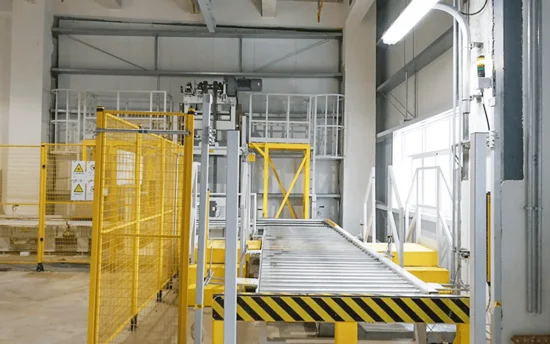
BASF serving the changing automotive industry needs
The previous conveyor system was not performing well with regular faults and problems (in existing building). Pallets would overshoot when transferring on RA decks and were not able to adjust the transfer speed to reach the production requirement. European companies must follow EU Machine Directives to protect employees from explosion risk in areas with an explosive atmosphere. A silicon free and explosion proof pallet conveyor system had been required. Therefore, the new production site was built to serve the China automotive manufacturing market and to meet developing industry needs.
Lödige Industries provided the customer with the design, manufacturing, installation, and commissioning of the silicon free and explosion proof pallet conveying system. The system is equipped with converter controlled motors, so the conveyors’ transfer speed can be adjusted to reach client‘s requirement. The remote controling ability enables BASF to check and control the system when necessary. In addition, all equipment supplied are silicon free and with the applicable ATEX certificates and Ex nA IIC T3.
The new plant enables BASF to produce thinners, primers, clearcoats and waterborne basecoats. The new pallet conveying system is used to transfer the components from 2nd floor to the ground floor and transfer back empty pallets to 2nd floor for other coatings loading. It was supported by a new automotive application center providing automotive manufacturers access to advanced R&D facilities, including a 3-D robot for coatings application at the BASF Innovation Campus Asia Pacific (Shanghai), by end of 2018.
About BASF
The Coatings division of BASF is a global expert in the development, production and marketing of innovative and sustainable automotive OEM and refinish coatings, as well as decorative paints. BASF creates advanced performance solutions and drive performance, design and new applications to meet their partners’ needs all over the world. BASF shares skills, knowledge and resources of interdisciplinary and global teams for the benefit of customers by operating a collaborative network of sites in Europe, North America, South America and Asia Pacific.
Facts and figures
Changing market demands for automotive production in China
- The automotive manufacturing market in China is on the rise.
- BASF Shanghai Coatings Co. Ltd. planned an investment to build a new, world-scale automotive coatings plant at the company's existing site at Shanghai Chemical Industry Park in Caojing.
- The customer required an expansion of world-scale automotive coatings plant with sufficient capacity. This required close collaboration with the plant operations to ensure safety, high throughput capacity, flexibility and convenience.
- The industry needs include the transition from solvent borne to waterborne coatings and from standard primer processes to integrated processes to reduce energy consumption of paint shops.
BASF Shanghai Coatings meeting the market demands
- The previous conveyor system was not performing well with regular faults and problems (in existing building).
- Lödige Industries provided the customer with the design, manufacturing, installation, and commissioning of the silicon free and explosion proof pallet conveying system.
- The new plant enables BASF to produce thinners, primers, clearcoats and waterborne basecoats. The new pallet conveying system is used to transfer the components from 2nd floor to the ground floor and transfer back empty pallets to 2nd floor for other coatings loading.